Unfinished Hardwood Flooring
+Pluses
- Widest range of colors and hues
- Widest range of species, grain and texture
- Widest range of design choices
- Square edge installation possible
-Minuses
- Requires an extensive sanding and finishing process
- Requires multiple days of having to stay off the floor during sanding and finishing
- Typically there is an odor associated with the polyurethane coatings
- Finish can be less durable than pre-finished
Unfinished wood flooring is the standard against which all wood flooring options are measured and compared. About 37% of wood flooring installed can be categorized as unfinished. In 2014 it was estimated that over 300 million square feet of unfinished wood flooring will be installed in American homes, and its popularity continues to increase each year.
Unfinished floors offer the widest range of species
Unlike pre-finished or engineered wood flooring, unfinished floors are available in almost any wood species you can imagine. From traditional choices like red oak and maple to the more unusual including Ipe, Sapele and Wenge, unfinished wood offers the widest range of choices. Different wood species don’t just offer color choices, they also offer widely different graining and variation which can transform a floor from a neutral canvas to a dramatic focal point.
(photo of floor that is a focal point)Unfinished wood floors can be stained or painted
Because unfinished floors can be stained or painted onsite, they offer the most staining and color choices. For example, start with a light colored, tightly-grained species like maple and bring in a dark stain. The result will be a seamless canvas that unifies several spaces and serves as the perfect backdrop to contrasting furniture, rugs or cabinetry. Alternatively, a painted wood floor can make an incredibly bold statement in a room. Painting has the added benefit of hiding imperfections and bringing in a range of colors that is not possible through staining.
Types of unfinished hardwood flooring
Unfinished wood flooring falls into three general types:- Strip flooring – The most common form of unfinished flooring, strip flooring is typically ¾” in thickness and typically 1 ½” to 3” in width. The strips vary in length, but all share a tongue-and-groove cut along the long edge that allows the boards to be locked together and blind nailed (nails are hidden by the edge) on top of a wood subfloor.
- Plank flooring – Plank flooring, popularly described, refers to wood that is cut in widths of 3” to 10”. Essentially, plank flooring is a wider version of strip flooring. Wide plank floors are becoming increasingly more popular, but because it is more difficult and less efficient to manufacture wide boards, it tends to be more expensive than strip flooring.
- Parquet flooring – Parquet floors vary in style and size and are typically made from individually cut slats that are pieced together to form geometric shapes. Held in place against a subfloor using nails or adhesive, parquet flooring can be expensive because of the time and expertise required.
Installation of unfinished wood flooring
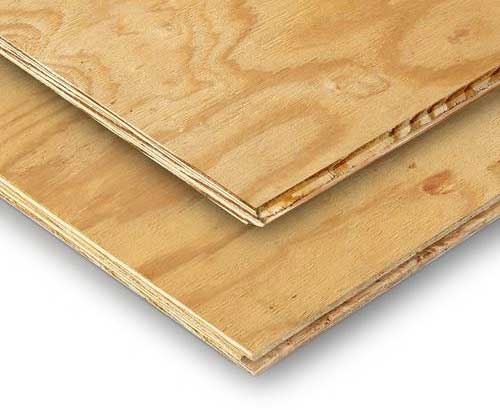
Sanding and finishing a wood floor
Once the unfinished flooring is installed, and stained if that’s the choice, three coats of polyurethane coating is applied to protect and add the desired depth of shine. While there are installers who continue to use oil-based finishes, Mr. Floor only uses a water-based polyurethane finish. The advantages to a water-based polyurethane include minimal emission of VOC’s, fast curing time, and excellent durability.